
Optimizations for aerospace industry: A new deviation label and the optimized workflow for profiles with different tolerance regions can be used especially for the inspection of the profile shape and position of an airfoil.Įvaluating the photogrammetry quality: Based on the precision computation of the individual reference points in the 3D view, conclusions on the quality of the entire measuring setup can be drawn, especially for expert analyses. With these functions, surfaces can be identified that can cause problems during demolding of a tool, for example, in casting processes.Įxtended analysis of surface defects without CAD data: In the GOM Software 2018, an estimated reference surface can be created to be able to distinguish defects from the real shape of the part more clearly. Inspection of draft angles: The inspection of draft angles extends the range of the inspection functions available to date.


Open data exchange: In addition to the existing import and export options, a compound of CAD patches, polygonized meshes and several stages can now be exported, for example, as G3D or STL files.Ĭalibration of the measuring setup during automated measurement: Using the new function, CAD data of the measuring object and, if necessary, of the fixture can be positioned exactly based on real data so that the measuring setup is calibrated for the project. Interactive presentation mode: The new, simple user interface enables interactions, such as rotating the part and configuring the legend, while the report pages themselves remain unchanged and thus protected.Įxtended import of CT data: Even if the volume data is larger than the main memory of the computer, it can be imported into the GOM Software 2018 and then polygonized.

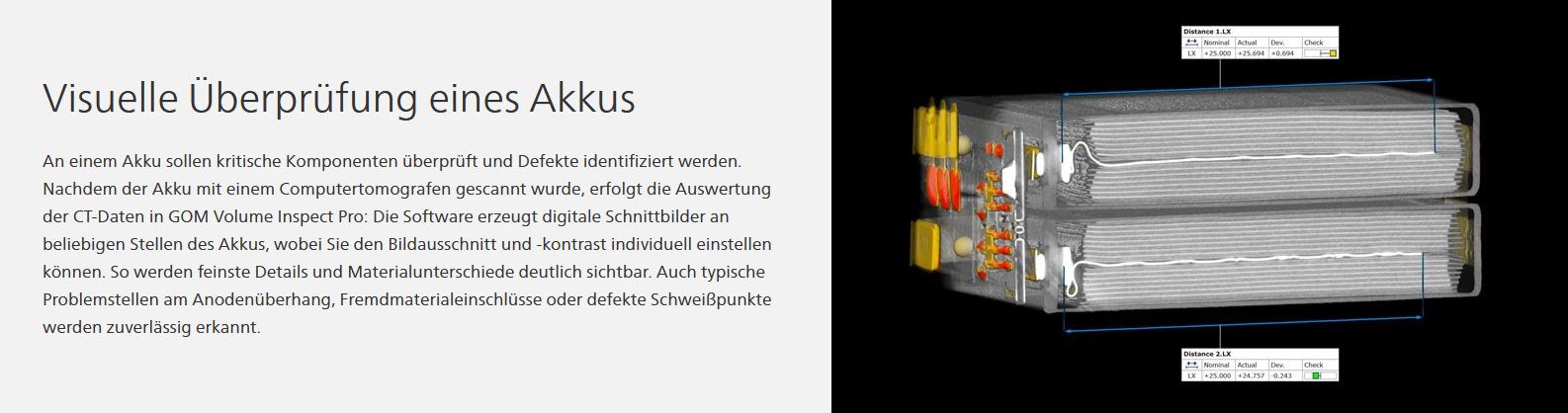
Augmented Reality: A new mode enables inspection results to be displayed directly on the real object and viewed on a tablet with an integrated camera or another mobile device with an external webcam, for example during audits.
